Leadership
Timken Service Engineers Triage and Treat Costly Equipment Challenges
Xavier Monachon was working through a high-stakes problem. He’d been called out to fix the propeller shaft on a ferry connecting the island of Corsica with mainland France. The competitor brand bearing had failed and a new Timken spherical roller bearing ordered.
When he arrived on board—plan, products and tools in hand—he discovered that the shaft clamp rings didn’t fit the existing housing.
“The ship can carry more than 500 passengers and 120 cars at a time, and it had to set sail in 12 hours,” recalls Monachon, a Timken service engineer based in Lyon, France. “Missing the deadline would have meant canceling at least one round trip, inconveniencing passengers and potentially costing the ferry operator €240,000 or more.”
To solve the problem, Monachon got creative, leveraging local connections to rapidly custom-modify the clamp rings for a correct retrofit. Because of his quick thinking under pressure, the ferry sailed on time and the customer ordered the same solution for additional ships.
Cool heads and an eye for the solution
Timken service engineers like Monachon often spend their days troubleshooting—using their expansive knowledge, mechanical skills and ability to improvise to keep equipment around the world in motion. Sometimes, it’s about addressing a small issue before it grows into a larger one. Other times, the problem is massive, catastrophic and extremely urgent.
Timken service engineers are experts when it comes to listening to customers in distress, identifying root causes and providing both quick fixes and long-term solutions. One day, they might be helping a pharmaceutical company improve bearing mounting practices in a critical pump application, so it can deliver medicine without delay. Another day, they might be recommending new assembly and fitting standards to increase uptime for a paper manufacturer, so they can keep toilet paper and facial tissue on the shelves.
“They are our eyes and ears in the field,” says Dragos Oprescu, Timken’s global manager of service engineering. “While our product and application engineers always design for the real world, our service engineers are there to solve problems when that world suddenly changes.”
Service engineers are the first to notice when isolated customer practices become industry trends. As they report their observations back to colleagues in other engineering roles, they help inform and shape future Timken product innovations.
For example, U.S.-based service engineer Scott Ickes recently noticed that many of his paper mill customers were seeing excessive moisture and insufficient sealing in press felt roller bearings. The resulting downtime was expensive, with a typical mill comprising 36 bearing positions affected by the same sealing challenge.
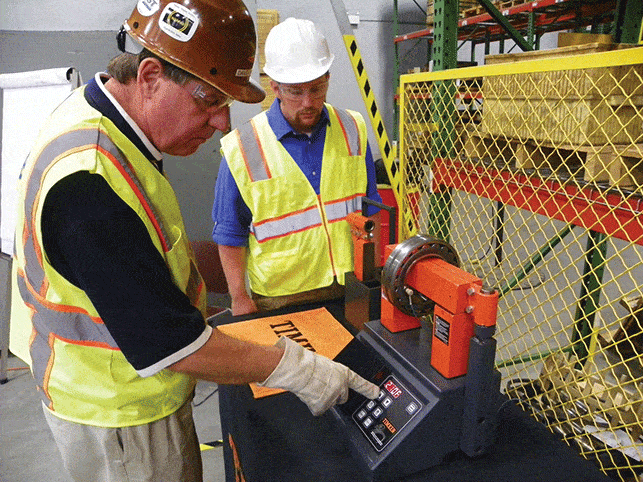
Service engineer Scott Ickes (right) realized that multiple mills he visited were experiencing equipment downtime due to the same issue.
Ickes raised the issue with Timken product engineers, and the collaboration that followed generated a spherical roller bearing solid block housed unit that significantly increased mill uptime.
“We run to the problem.”
The scope of Timken’s service engineering capabilities has broadened over the years as the company has added to its family of brands and expanded the markets it serves. Today’s network of Timken service engineers includes skilled, field-ready professionals with expertise across a wide spectrum of power transmission scenarios.
Last April, Timken Power Systems (TPS) Northeast General Manager Rich Chrzanowski woke up to a 2 a.m. phone call. One of two nuclear power plants providing electricity to customers in the northeastern United States had gone down after an internal lubrication error caused massive failure in a Philadelphia Gear clutch. The clutch, which had operated for years without issue, was a critical component in a steam turbine the size of an American football field, essential for delivering power to millions of customers.
The call set in motion an extraordinary response. Philadelphia Gear service engineers and suppliers collaborated around the clock over a holiday to disassemble, ship, repair, return and reinstall the clutch. They accomplished their mission in a matter of days, rather than the weeks it would have taken in a non-emergency situation.
“Our philosophy is we run to the problem,” says Chrzanowski. “We treat it like it’s our own operation that needs to get back online, and that sets us apart.”
Timken Power Systems brings that same desire to go above and beyond to the wind energy industry, with a highly-trained field service team focused on corrective services for large turbines.
In one recent case, the H&N Wind team—also a part of TPS—traced the cause of several generator failures at a wind operator’s site to a common problem with damaged wye rings. Wye rings serve as the electrical connection between the generator and rotor coil packs that essentially act as the “ignition” for a wind turbine.
The technicians, with their unique mix of electrical and mechanical engineering knowledge, performed up-tower assembly of upgraded wye rings, bearings and other components to restore service to several generators. Their work helped the wind operator avoid extended equipment downtime and ensured uninterrupted power service for the households they served.
A deep commitment to service
While it’s typical for Timken associates to contribute beyond their formal job descriptions, nowhere is that more prevalent than on the global service engineering team.
Service engineers create mounting manuals and setting and lubrication instructions for new bearings before they’re installed. During installations, they go on site to help with those processes and to train customer teams on how to apply them correctly. In the process, they enhance equipment performance as well as the safety of equipment operators and maintenance teams.
Service engineers also help get Timken solutions safely from the factory floor to their application homes. “We advise on how to place them in boxes or on pallets to make sure they travel well through the logistics chain,” says Oprescu.
Shipping becomes a real challenge when parts are extreme in size or weight. The chain of logistical decisions can be critical when you’re talking about a multi-ton roll neck bearing for a steel mill, an ultra-large wind turbine mainshaft bearing, or a gear drive on a naval ship. When you’ve worked hard to design and build the exact right solution, the last thing anyone wants to hear about is shipping damage.
“When the customer receives the product, we’ve already considered how they’re going to open it, handle it, and install it correctly,” says Oprescu. “Our input essentially impacts every touchpoint in a product’s lifespan, from initial design to replacing it when its service life comes to an end.”
Seasoned service engineers also mentor new service engineers in the field to pass their decades of knowledge on the next generation. That field experience is critical. Unlike application engineers, who specialize in particular industries, service engineers serve a mix of customers within their territories.
“There’s no easy way to learn everything there is to know. People who have been doing it for 40 years still learn something new every day,” says Oprescu. “It takes a lot to be a service engineer, but their continuous on-the-job learning benefits our customers—and ultimately the public they serve—every time they make a service call.”
Last Updated: 2023/07/21
Published: 2020/07/27