Timken® EnviroSpexx™ Energy Efficient Roller Bearings
Timken EnviroSpexx roller bearings are designed to increase efficiency and reduce energy consumption, which affects carbon footprint. These bearings are designed with geometries that minimize rotational torque for maximum system efficiency. Optimized geometry can lead to torque reduction, resulting in an overall decrease in the amount of electricity required to operate equipment or machinery. By incorporating Timken EnviroSpexx roller bearings into your equipment, you can reduce energy costs and carbon emissions.
Rich History in Energy Efficiency
Timken engineers have leveraged knowledge gained through decades of producing fuel-efficient bearings for the automotive industry, as well as 125 years serving industrial markets, to create its energy-efficient bearing offering. We apply knowledge to optimize system weight and bearing energy consumption and torque to help conserve energy within a wide range of applications.
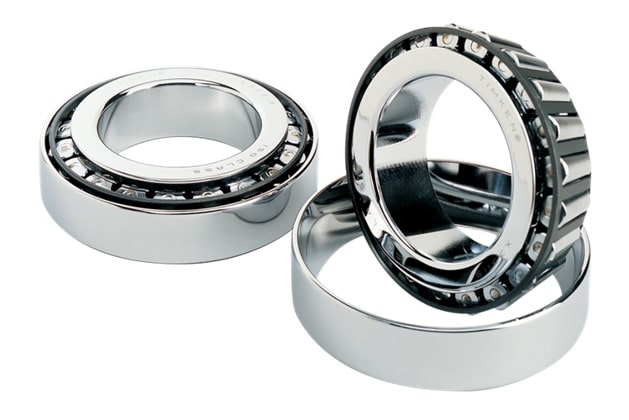
Advantages
Meet Your Environmental Goals
EnviroSpexx roller bearings are specifically designed to provide more energy efficient solutions to help you meet your environmental goals.
Torque and Electricity Reduction
Optimized internal geometry, leads to torque reduction, and at the end of the day, an overall decrease in the amount of electricity needed to operate a wide range of applications globally.
Optimal Bearing Internal Geometries
125 years of knowledge and experience, Timken engineers the optimal bearing internal geometries that balance torque and fatigue life.
Emission Reduction
By reducing the amount of electricity needed to operate equipment, overall emissions can also be reduced, helping to move your corporate social responsibility (CSR) initiatives forward.
Broad Roller Bearing Portfolio
The EnviroSpexx portfolio includes specially designed roller bearings commonly used in industrial applications, such as gear drives, pumps and compressors.
Energy and Emission Savings in Industrial Applications
Compressor Application
- Bearing efficiency increases by 25%
(current vs. enhanced)
- Current bearings = 4.0 N-m torque each, Enhanced Bearings = 3.0 N-m torque each
- Two tapered roller bearings supporting the compressor shaft
- Compressor Driven by an electric motor operating at 3000 RPM
- Operational Time of Consideration: 5 years
- Customer Location: USA
- $0.17 KWh (based on US average)
- 852.3 lbs CO2 per MWh
(source: US EPA, national avg.)
Source for calculations: EPA
Calculations |
---|
Torque Savings with Enhanced Product = (2 * 4.0 N-m) - (2 * 3.0 N-m) = 2.0 N-m |
Energy Consumption (Q =k*N*M) = .105*3000 RPM * 2.0 N-m = 630 W = .630 KW |
Lifetime Energy Consumption = .630 KW * (24 hrs/day * 365 days/yr * 5 years) = 27,594 KW = 27.6 MWh |
Energy Cost Savings/Lifetime=
.630KW * $0.17 *
(24 hrs/day *
365 days/yr * 5 years) =
$4,691 saved
Emissions Savings:
852.3 lbs CO2 per MWh * 27.6 MWh =
23,523 lbs CO2 saved
(10,670 kg CO2)
Pump Application
- Bearing efficiency increases by 10% (current vs. enhanced)
- Current bearings = 3.0 N-m torque each, Enhanced Bearings = 2.7 N-m torque each
- Two tapered roller bearings supporting the pump shaft
- Pump driven by an electric motor operating at 1800 RPM
- Operational Time of Consideration: 5 years
- Customer Location: USA
- $0.17 KWh (based on US average)
- 852.3 lbs CO2 per MWh
(source: US EPA, national avg.)
Source for calculations: EPA
Calculations |
---|
Torque Savings with Enhanced Product = (2 * 3.0 N-m) - (2 * 2.7 N-m) = 0.6 N-m |
Energy Consumption = (.105 * 1800 RPM * 0.6 N-m = .113 KW |
Lifetime Energy Consumption = .113 KW * (24 hrs/day * 365 days/yr * 5 years) = 4,949 KWh = 4.95MWh |
Energy Cost Savings/Lifetime=
.113KW * $0.17 *
(24 hrs/day *
365 days/yr * 5 years) =
$841 saved
Emissions Savings:
852.3 lbs CO2 per MWh * 4.49 MWh =
4,219 lbs CO2 saved
(1914 kg CO2)
Geardrive Application
- Bearing efficiency increases by 10% (current vs. enhanced)
- Current bearings = 6.6 N-m torque each, Enhanced Bearings = 6.0 N-m torque each
- Two tapered roller bearings per shaft x 3 shafts = 6 total bearings
- Gearbox driven by an electric motor operating at 1800 RPM
- Operational Time of Consideration: 5 years
- Customer Location: USA
- $0.17 KWh (based on US average)
- 852.3 lbs CO2 per MWh
(source: US EPA, national avg.)
Source for calculations: EPA
Calculations |
---|
Torque Savings with Enhanced Product = (6 * 6.6 N-m) - (6 * 6.0 N-m) = 3.6 N-m |
Energy Consumption (Q =k*N*M) = .105*1800 RPM * 3.6 N-m = .680 KW |
Lifetime Energy Consumption = .680 KW * (24 hrs/day * 365 days/yr * 5 years) = 29,784 KWh = 29.8 MWh |
Energy Cost Savings/Lifetime=
.630KW * $0.17 *
(24 hrs/day *
365 days/yr * 5 years) =
$5,063 saved
Emissions Savings:
852.3 lbs CO2 per MWh * 29.8 MWh =
25,398 lbs CO2 saved
(11,520 kg CO2)
Resources
Get in Touch - EnviroSpexx™ Energy Efficient Roller Bearings
For more information on Timken® EnviroSpexx™ Energy Efficient Roller Bearings, fill out this form.
*Required field