Responsabilità
Costruire un futuro più sostenibile
L’esperienza di Timken contribuisce a una miriade di tecnologie sostenibili, dai cuscinetti ad alta densità di potenza per migliorare l’efficienza dei veicoli elettrici alle soluzioni di controllo del movimento di precisione che rendono possibile l’impiego di energia solare. Eppure l’impegno ambientale dell’azienda parte dalle operazioni di produzione in tutto il mondo.
Lì, la risoluzione dei problemi tecnici di Timken aiuta l’azienda a gestire impianti di produzione più sostenibili che funzionano in modo più efficiente e supportano comunità più sane. Marius Mazur, responsabile dei sistemi di ambiente, salute e sicurezza (EHS) di Timken a Sosnowiec, in Polonia, spiega in che modo gli innovativi compressori d’aria nel suo stabilimento contribuiscano a realizzare prodotti, riscaldare edifici e ridurre le emissioni di gas serra.
“In sostanza, catturiamo il calore generato dai compressori e lo ridistribuiamo in tutta la struttura durante i mesi freddi”, afferma Mazur, che è entrato alla Timken 17 anni fa come operatore della qualità e ha ricoperto posizioni in ambito di qualità e gestione dello stabilimento. “Riduce del 17% la nostra produzione annuale di gas serra generata dal riscaldamento”.
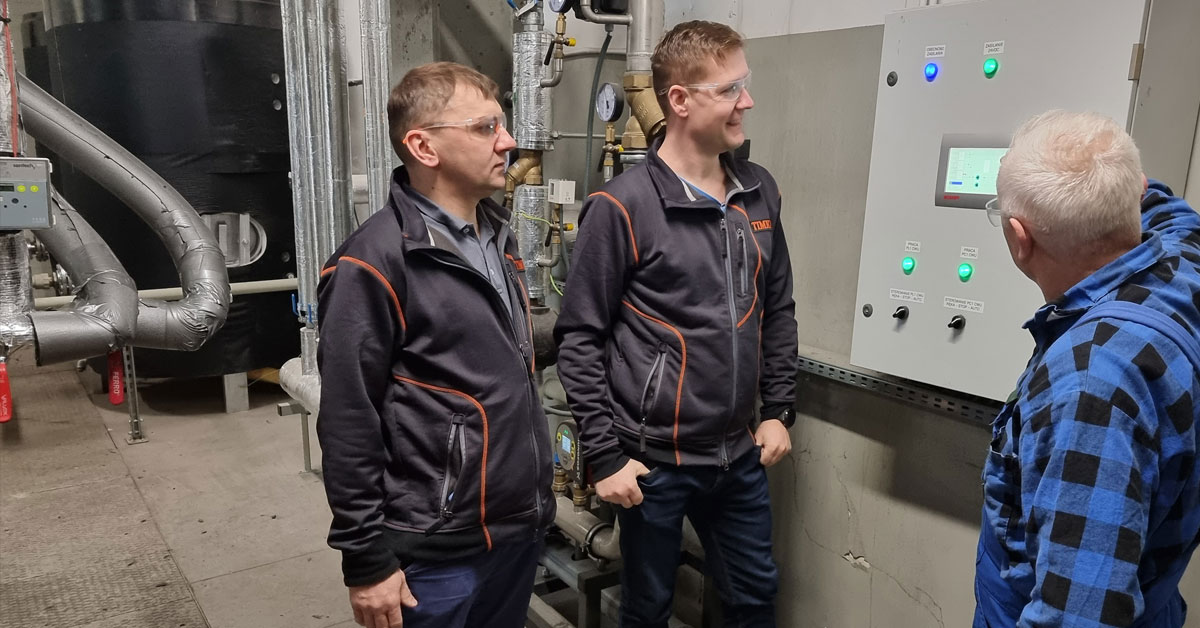
Tomasz Pniak, ingegnere dell’impianto, Mariusz Mazur, responsabile – Sistemi EHS, e Andrzej Wątor, tecnico di manutenzione, esaminano il sistema che raccoglie l’acqua riscaldata da ridistribuire in tutto l’impianto.
“Abbiamo un punto di vista ugualmente ambientale ed economico. Siamo più rispettosi dell’ambiente e utilizziamo meno risorse per operare in modo più efficiente in tutta la struttura. Piccoli miglioramenti insieme fanno una grande differenza per la nostra struttura, la comunità e l’ambiente”.
Marius Mazur
Responsabile EHS
‘Energia termica più che sufficiente’ generata dalle apparecchiature
Timken è impegnata nei confronti della responsabilità sociale d’impresa e l’esperienza specializzata dell’azienda e il desiderio di essere custodi positivi dell’ambiente le hanno permesso di promuovere soluzioni che riducono l’impatto ambientale della produzione, a livello globale e locale, attraverso le più recenti innovazioni di processo e attrezzature.
Lo stabilimento di Sosnowiec di Timken ha utilizzato i compressori d’aria per uno scopo fondamentale: alimentare le apparecchiature utilizzate in diversi processi di produzione dei cuscinetti. Inizialmente, la struttura utilizzava compressori d’aria raffreddati ad acqua per supportare le esigenze di potenza elevata delle apparecchiature.
Da allora, sono emerse altre innovazioni del compressore d’aria che consentono di risparmiare acqua ed elettricità offrendo al contempo una maggiore efficienza operativa. Riconoscendo questo, il team della struttura ha iniziato a ripensare al modo in cui utilizza i compressori d’aria. Potrebbe essere utilizzato un sistema alternativo per riscaldare l’edificio? Si potrebbero utilizzare meno elettricità e acqua? È possibile operare in modo più efficiente? La risposta a tutte queste domande era “assolutamente”.
Alcuni mesi fa, lo stabilimento di Sosnowiec è passato dai compressori d’aria raffreddati ad acqua ai compressori d’aria avanzati raffreddati ad aria. Queste unità utilizzano l’aria anziché l’acqua per il raffreddamento e generano calore significativo nel processo. I circuiti raffreddati ad aria riducono l’aria calda con una ventola e un radiatore. La perdita di calore viene quindi recuperata e ridistribuita come riscaldamento sostenibile ed economico in tutto l’edificio.
“I nostri nuovi compressori raffreddati ad aria producono energia termica più che sufficiente per tenere tutti al caldo”, afferma Mazur. “I dipendenti ci hanno effettivamente chiesto di abbassare il riscaldamento, e lo abbiamo visto come un feedback davvero positivo”.
Energia verde, produzione più efficiente
Il commutatore utilizza anche meno elettricità, riducendo ulteriormente l’impronta di carbonio del sito ogni anno. Inoltre, i nuovi compressori d’aria contribuiscono a una maggiore efficienza di produzione.
Invece di essere installate in un’unica stazione come le unità originali raffreddate ad acqua, le tre unità raffreddate ad aria funzionano indipendentemente per alimentare le apparecchiature in tre diverse zone della struttura di 50.000 metri quadrati. Questa decentralizzazione garantisce che la maggior parte dei processi di produzione possa continuare a funzionare anche se un compressore d’aria e le apparecchiature nella zona corrispondente vanno offline.
L’iniziativa ha avuto un tale successo che Timken non vede l’ora di implementarla per ridurre il consumo di energia e le emissioni di gas serra in altre sedi.
I miglioramenti incrementali hanno un grande impatto
Oggi lo stabilimento di Sosnowiec utilizza l’energia termica in eccesso non utilizzata per il riscaldamento dell’impianto per riscaldare l’acqua destinata al consumo sanitario, come lavaggio mani e pulizia. Nel 2020 la struttura ha utilizzato a tale scopo 200 gigajoule di energia; l’anno scorso ha utilizzato solo 11 gigajoule.
Mazur osserva che altre iniziative recenti hanno incluso una migrazione all’illuminazione a diodi a emissione di luce (LED) e l’aggiornamento delle pompe delle stazioni di raffreddamento per una maggiore efficienza elettrica.
“Abbiamo un punto di vista ugualmente ambientale ed economico”, afferma. “Siamo più rispettosi dell’ambiente e utilizziamo meno risorse per operare in modo più efficiente in tutta la struttura. Piccoli miglioramenti insieme fanno una grande differenza per la nostra struttura, la comunità e l’ambiente”.
Il team EHS globale di Timken collabora con gli impianti di produzione locali per raccogliere e analizzare i dati per un quadro completo sul modo in cui gli elevati standard EHS dell’azienda vengono riprodotti nella vita reale. Scoprite di più qui.
Published: 2022/05/11