Innovation
The Right Material for Every Application
Before he came to the Company five years ago, Lee Rothleutner’s experience with Timken was limited to the ranch in Nebraska where he grew up. The black and orange box was a common sight on the workbench as he and his dad swapped out bearings on the tractor.
After starting in Timken’s research and development (R&D) department, Rothleutner’s perspective shifted pretty dramatically. “I realized exactly the breadth of work Timken does,” he says. “I’m a PhD metallurgist, and there’s nothing more exciting than having access to laboratories where I can do almost any metal heat treat process I want.”
Today, as manager of materials R&D, he brings that mentality to his team. “I take this massive book off my shelf, ASM Handbook, Volume Four,” he says. ASM International is the 108-year-old global engineering community known for gathering and disseminating materials knowledge. Volume Four is titled, Heat Treating.
“I tell them I want us to have a position on every single heat treatment process in that book,” he says: “Whether it works for us, doesn’t work, and why. If it works, I want the process and means to be able to implement it.”
The ingredients of an ingredient brand
Rothleutner was initially hired to help drive development of Timken’s seamless induction hardening process for ultra large-bore wind turbine main shaft bearings. He had great success there and was promoted to lead the material conversion group before taking on his current position.
As a result of his wind energy work, Rothleutner spent a lot of time in Romania, working with the Ploiesti Engineering Center of Excellence team. Today, he and his team also play a role in the advanced through-hardening processes and technologies featured in the nearby Prahova plant. “There, we use a process called ‘austempering,’ which makes bainitic steel,” he says.
The team has also made strides with coatings technologies in the past few years, doubling capacity in 2020. “There’s a huge demand for that right now, and Vikram Bedekar, our group leader in that area, has done tremendous work,” says Rothleutner.
The materials team is also charged with optimizing case carburization processes — technology that goes back to Timken’s original 1897 patent. “We know that technology extremely well, so we know where it fits and where other processes are better-suited,” says Rothleutner.
Right ingredient, right application
Timken engineered solutions involve, at the root, identifying the right ingredients and the right recipe for each application. “Customers come to us with a specific set of properties they want to hit,” says Rothleutner. “We put together the chemistry and the structure.”
Getting there is a team effort, with application engineers taking the lead. R&D gets involved when the solution requires chemistry and structure that go beyond standard Timken processes, but the materials choice often comes down to application conditions. Applications that see the harshest shock loading and debris, such as continuous casting lines in steel mills, require case carburized steel — the hardest of the hard. For those with good lubrication in less extreme environments, bainitic steel can perform equally well.
Today, for example, one mining and construction equipment manufacturer is converting Timken differential bearings on wheel loaders from case carburized to through-hardened steel. Agricultural implement transmissions increasingly feature through-hardened bearings, as well.
“We’re leveraging our century of experience with case carburization to understand the limitations with different processes,” says Rothleutner. “We have the testing, we have the data, so we know exactly where other processes can provide equally high performance with less resources.”
In the case of wind turbine mainshaft bearings, case carburization cycles would have added 100 hours or more to the manufacturing process, while seamless induction hardening does the same thing in about two hours. “You’re talking about a 50% reduction in the time to produce a bearing, so customers increasingly write it into their specifications,” he says.
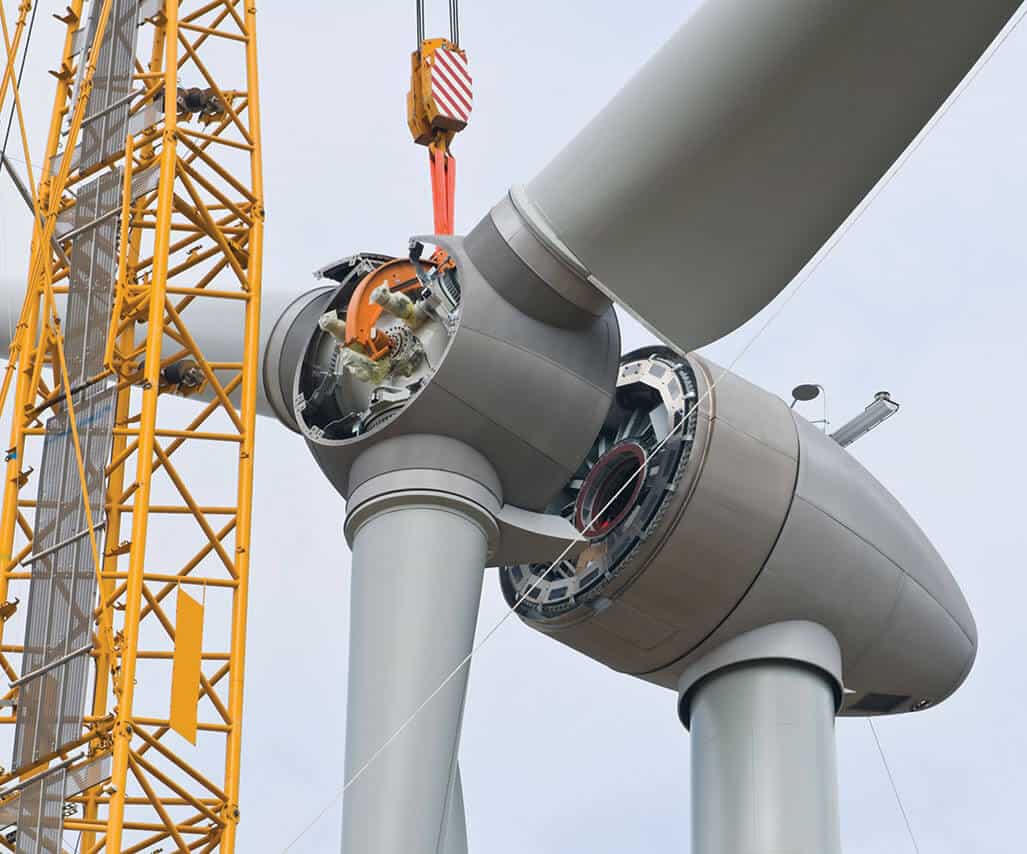
“I take a lot of pride in my work in the renewable energy sector, and I know that’s been a big driver for many people I’ve hired. Friends at some of the most well-known renewables companies in the world are amazed at the work we do here with wind turbines and ridiculously large bearings. They know the challenges there.” Lee Rothleutner
Manager of Materials R&D
Advanced modeling, quicker solutions
The team is also evaluating 3D metal additive manufacturing capabilities, using 3D printers to create prototypes, demonstration pieces, and customized tooling components. “3D is a hot topic in the industry, and we’re evaluating where exactly it fits for us,” says Rothleutner.
For now, the biggest bang for the buck is coming from the team’s effort to advance process and finite element modeling. “Gathering data about our heat treat processes helps us be more predictive — to model a solution before we make a hard prototype and to predict how the product will behave in the future,” he says.
Advanced modeling also helps the team interface more directly with customers, so they can understand application nuances more clearly and land on solutions more quickly.
A metallurgical community
Materials research is complex — but it’s also very rewarding for a group of people who enjoy what happens when you combine chemistry, structure, and properties in a lab where any average day could include a major metallurgical breakthrough.
“Right now, we’re working on optimizing new carburizing and plasma nitriding processes, and other fun projects for different segments of the business,” says Rothleutner. “We’re looking at wind turbine gearboxes, some aerospace alloys, some off-road solutions for extreme conditions.”
The constantly evolving work streams and the sense of participating in projects that further efficiency and progress — keeps them engaged and coming back to the lab every day.
Timken R&D worked directly with customers to develop ES302 wear-resistant coatings. Read how the results dramatically extend lifespans for applications in wind energy, agriculture, aerospace and others.
Last Updated: 2021/08/6
Published: 2021/04/25