Sustainability
Global Initiative: Single-Use Plastics Reduction
Timken is currently carrying out a global initiative to drive down single-use plastics across its business, including vendors and third-party logistics providers. The company has started in its own facilities, using recyclable paper to replace plastic dunnage — the packing material used to protect products during shipping. Jamie Milobar, manager of global environmental affairs, and Kim Rudy, manager of global packaging, transportation and warehousing, are leading the Timken effort.
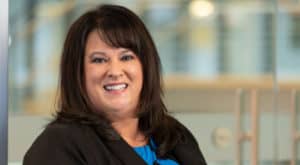
Jamie Milobar, environmental affairs
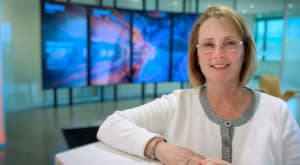
Kim Rudy, packaging, transportation & warehousing
Why is Timken focusing on this initiative?
Milobar: It’s estimated that the world makes more than 400,000 million tons of plastics annually. And plastic packaging accounts for half of all plastic waste — much of which ends up in landfills, in oceans and waterways, and throughout our communities as litter. Together, we can all do better. We have to in order to sustain our environment, communities and future generations.
Rudy: The plastic dunnage initiative was selected as a priority because it touches our entire global manufacturing and distribution footprint. Every product we make is packaged and shipped in some way. It’s also about helping our customers be more sustainable, because how we package products determines how much they will be able to reuse or recycle the
materials we send them.
How much plastic will the dunnage initiative take out of the environment?
Milobar: We expect to annually prevent about 13,550 cubic feet of single-use plastic from entering U.S. landfills alone. That’s the equivalent of 70,000 bowling balls. The positive impact will be even greater as we bring all our global facilities onboard.
How are you implementing it?
Rudy: A Timken team made up of people in environmental affairs, packaging, engineering, supply chain and manufacturing have all played a role. Making the switch is more complex than simply replacing materials. We needed to ensure that a recyclable, biodegradable paper was a suitable packing alternative that could still preserve the integrity of our products during shipping. We performed intensive research, analysis and testing before installing paper dunnage equipment in three initial U.S. facilities. We are now in the process of totally implementing it in all production facilities worldwide, across our entire product portfolio.
What is the most rewarding aspect of leading a global sustainability initiative?
Rudy: We’ve had the right technical teams involved to find the right solution, and it’s been rewarding to see what can happen when a team works together toward a common goal. We’ve all been motivated by the fact that it’s the right thing to do for our environmental future.
Milobar: For me, it feels great to do work that I know is going to be part of a global solution — something that impacts not just me, or Timken, but everyone. When we see the impact of a single project like this one, it inspires us — and hopefully others — to keep going. Because there is no one big solution to sustain our environment. It takes all of us making smaller, manageable changes that all add up to a greater positive impact.
Last Updated: 2021/08/19
Published: 2020/10/28