Innovation
Quantum Leaps
Built over a 10-year period, in collaboration with more than 10,000 scientists, the Large Hadron Collider (LHC) is the world’s largest, most-powerful particle accelerator. It was developed at the European Organization for Nuclear Research (CERN) to answer fundamental questions about the existence and makeup of the entire universe.

At the heart of the Large Hadron Collider, bright yellow custom manipulators featuring SPINEA reduction gears facilitate the connection of 1,800 large pieces of pipe containing powerful magnets and instrumentation within the tight space of the collider’s tunnel. (Image: CERN)
The LHC has made several advancements in physics, including the first detection and observation of collider neutrinos particles this August, an accomplishment that will open new avenues of research for experimental physicists, and SPINEA industrial motion solutions helped make it possible.
A Complex Complex: Installing the LHC
The LHC is housed in a 27-kilometer-wide ring, 100 meters beneath the Swiss Alps. When CERN engineers began installing collider instrumentation in 2008, they ran into the challenge of assembling parts in a very confined, hard-to-reach space. SPINEA, a leading manufacturer of highly engineered cycloidal reduction gears and actuators based in Slovakia, had the solution.
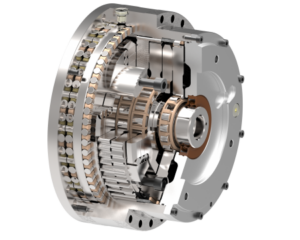
SPINEA’s TwinSpin® high-precision gears accurately position quadrupole magnets inside CERN’s Large Hadron Collider (LHC),the world’s largest, most-powerful particle accelerator.
“The collider is basically a ring-shaped tunnel with dipole magnets that are 49 feet (15m) long, and each weigh more than 30 tons,” says Slavomir Lesko, SPINEA sales director. “There wasn’t any room for heavy-duty lifting equipment like cranes, which made connecting tubes and other essential infrastructure nearly impossible.”
Using information from CERN and one of its collider equipment suppliers, SPINEA engineers performed their own calculations and designed high-precision cycloidal gear for the transfer equipment called “manipulators”.
Singularly engineered reduction gears featuring high load capacity, high precision and a compact design allowed the manipulators to connect 1,800 large pieces of pipe containing powerful magnets and instrumentation within the tight space of the collider’s tunnel.
When Precision is Paramount
Today, CERN continues using SPINEA’s gear for proper control, parameter setting and precision maintenance of particle accelerators at the facility.
Inside the LHC, two high-energy particle beams in tubes travel at near the speed of light, guided by thousands of superconducting electromagnets, before they are made to collide.
“Imagine two needles, one coming from Europe and the other from North America, and they both must extend across the Atlantic and hit each other exactly in the middle. That gives you an idea of how precise a solution must be.”
Slavomir Lesko
SPINEA sales director
“Imagine two needles, one coming from Europe and the other from North America, and they both must extend across the Atlantic and hit each other exactly in the middle,” Lesko says. “That gives you an idea of how precise the beams, and our gear solution, must be.”
There’s little room for error. From the scientific method itself to all the components in the extraordinary equipment facilitating it.
SPINEA’s TwinSpin® high-precision gears, accurately position the quadrupole magnets that induce approaching beams. The more aligned the magnets are, the more the beams collide — leading to more successful experiments. The SPINEA solution helped CERN scientists reduce the diameter of LHC proton beams from a millimeter down to 16 micrometers [0 .06 mm].
Lesko notes that the TwinSpin solution has provided reliable precision and long-lasting performance. “When I visited CERN last year, I expected there might be some replacement opportunities, but there weren’t … unfortunately,” he quips. “Because every gear we originally provided was still working properly after 15 years.”
Industrial Motion Solutions Across an Array of Applications
SPINEA products are found in an increasing range of applications
Learn more about how Timken helped create the world’s largest telescope.
Published: 2023/09/22